Some of the links below are affiliate links, meaning, at no additional cost to you, I will earn a commission if you click through and make a purchase.
In addition to my brewing, when I’m not working on some aspect of the house or the homestead, I like to spend time in the wood shop. I’m most successful at turning pieces of wood into big piles of sawdust, but now and again I’ll turn out something I’m willing to show to others. Once in a while, I can even repeat the process, and (after much practice) come up with something I truly like.
This was originally the case with my lathe-turned bowls and cups. My earliest examples, from when I was using a cheap drill-powered “lathe”, and didn’t really know what I was doing, were clunky, at best. I don’t believe any of those pieces still exist.
About four years ago, after a ten-year hiatus, I got myself a better lathe. This one was still cheap, and had its own idiosyncracies, but it had enough power, and stayed on-axis well enough, to let me refine my turning a bit more. After a bit of practice, and learning more about technique and process, I started producing somewhat more usable items.
Then, in early 2016, I went all-out and got a name-brand lathe. This was a step up in terms of being able to find accessories, in terms of the solidity of the lathe bed, and in terms of the power and speed of the motor. (It was also whisper quiet, relative to the old one!) I also went the route of getting a lathe bed extension, which allows me to turn spindles up to about 42″ in length. So, in addition to my usual bowls and cups, I now have the ability to turn the longer parts of chairs.
When I turn bowls, I base them mostly off of finds from Novgorod and/or York excavations. The Russian vessels I like because my SCA persona is Russian, for one, and for two, they’ve got generally the widest variety of things, ranging from small cups and salt-cellars up to really large serving bowls. The York finds are really well documented, but less extensive. Then I’ve got a few drawings, mostly in singles or pairs, from a couple of other finds. Exeter, for instance, provided one of my favorite styles: a “conic section” bowl with straight sides and a flat bottom.
I try to keep a selection up on my Etsy site (Holmgard Trading);
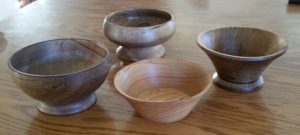
my inventory usually shows mostly as cups and small bowls, but I’ve got a few larger ones “in the back,” and I’m happy to turn more, especially if you’ve got a picture or a line drawing from an actual find. My main limiting factors are time, wood availability, and that I can only go as big as about 12″ in diameter. That said, if you’re interested in something, email me, or hit me up in my shop–I’m happy to see what I can do.
If you visit the shop, you’ll see that I’ve been branching out a little from just wood. At present, I’ve got a series of bone nalbinding needles. I’m hoping to get some “regular” sewing needles done up, as well, but they’re a little tricker to make. Eventually, I intend to do a few bone combs, as well. They’re problematic not for their size, like the needles, but more for making sure everything goes together correctly. I’ve not had luck with them yet, as things tend to go out-of-alignment, or (worse yet) crack at inopportune moments.
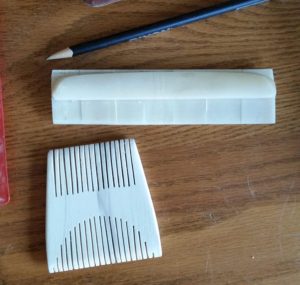
For handwork, lately, I’ve been trying out wooden combs. They seem about as common, in the Novgorod archaeological record. The process is similar to the bone versions, at least where the “fiddly bits” (the teeth) come in. One difference, though, is that if I mess up and crack a piece of wood, I’m not out that much. Scrap wood for combs I have, but the bones are harder to come by. Enough practice with the wood ones, I figure, and I’ll try tackling the bone ones again.
While I’m talking about bones, I’d really like to try something more complex with them, at some point–maybe a buckle or the like. I have plans for some small pendants, as well.
This, of course, isn’t the entirety of what keeps me busy–just a small sampling of the various wood crafts that I work on regularly. I’ll come back to this topic later, and take a look at some of my source material, as well as do a bit of how-to. Please sign up to the email list for updates, and post any questions in the comments below!